Towards digital metal additive manufacturing via high-temperature drop-on-demand jetting
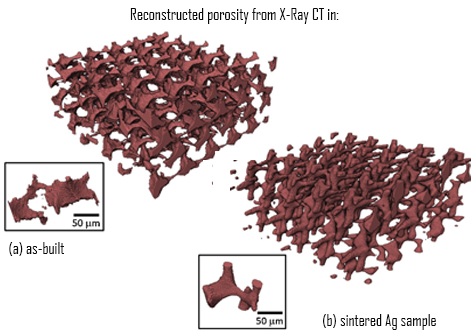
Drop-on-demand jetting of metals offers a fully digital manufacturing approach to surpass the limitations of the current generation powder-based additive manufacturing technologies. However, research on this topic has been restricted mainly to near-net shaping of relatively low melting temperature metals. Here it is proposed a novel approach to jet molten metals at high-temperatures (>1000 °C) to enable the direct digital additive fabrication of micro- to macro-scale objects. […] The research shows that by a careful choice of the jetting strategy and sintering treatments 3D structures of various complexity can be formed. This research paves the way towards the next generation metal additive manufacturing where various printing resolutions and multi-material capabilities could be used to obtain functional components for applications in printed electronics, medicine and the automotive sectors.