Fibre misalignment and breakage in 3D printing of continuous carbon fibre reinforced thermoplastic composites
Continuous carbon fibre-reinforced polymer (CCFRP) composites have been increasingly used in airframes and other high-end industrial products due to their superior mechanical properties such as high strength-weight and stiffness-weight ratios […] Additive manufacturing (also known as 3D printing) has shown potential to fabricate continuous fibre-reinforced composites with highly complex shapes in both 2D and 3D. Among them, Fused Filament Fabrication (FFF) 3D printing melts and deposits small thermoplastic filament (usually with 1k fibre tows) layer by layer to create the composite parts.
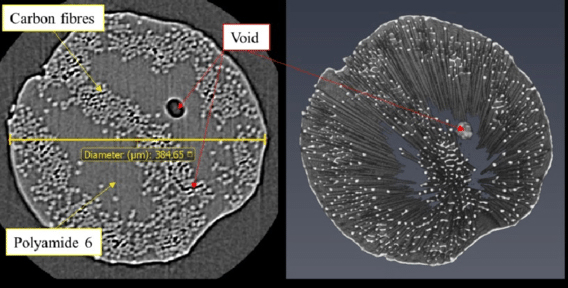
This paper investigates the formation of manufacturing induced fibre misalignment and breakage during fused filament fabrication (FFF) 3D printing of 1 K continuous carbon fibre filament. Single stripes at various turning angles and curvatures are printed by a desktop printer Prusa i3 using a specific brass nozzle and characterised using X-ray computed micro-tomography (µCT) and optical microscopy.