Defect detection in 3D printed carbon fibre composites using X-ray Computed Tomography
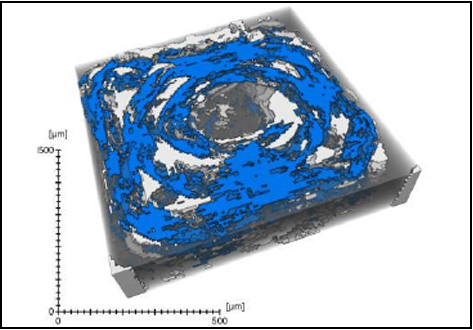
X-ray Computed Tomography (X-ray CT) has become a vital tool for product quality inspection. The X-ray CT analysis of 3D printed composites, with a layer-by-layer structure of carbon fibre/polyamide and polyamide plies, demonstrates how the void content increases with an increasing number of consecutive carbon fibre layers. Not only the void content, but also the pore
network complexity increases, as more pore types are introduced into the sample. The PolyAmide (PA) matrix has an average void content of 6%, consisting of interbead channels with strong anisotropy. Alternating a carbon fibre layer with two polyamide layers slightly increases porosity (6.8% on average), as both inter- and intrabundle porosities are now present. It was found that the premature cutting of the carbon fibre bundle results in a large void at the end of the print path, while the start of the path is also associated with voids and an interruption of the PA wall layers. Full carbon fibre layering sections introduce additional large voids (average porosity of 9.7%), as the carbon fibre bundle cannot fully move into the corners of the polyamide wall layers.